The Diesel Cycle consists of four stages.
1. Air is drawn via air filter into the intake stroke.
2. Air is adiabatically compressed to a high pressure and high heat during the compression stroke.
3. Diesel is injected into high pressure, high temperature cylinder space. The fuel ignites instantly and expands rapidly forcing the piston down- which is the power drive force- in the power stroke.
4. The piston compresses the exhaust gas to clear the cylinder space for the repeat action of stage. This is called the exhaust stroke.
In modern diesel engines, these functions are electronically controlled.
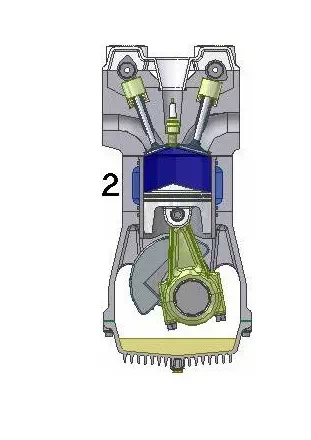
Camless technology
Electronics were first used to control fuel injection timing and quantity in diesel engines. In addition to this, camless technology also manages air in the combustion process by infinitely varying the valve timing. This improves drivability, reduces weight, and decreases emissions.
Presently camless diesel engine production is in the development stage. International Truck and Engine Corp. has recently unveiled a camless diesel engine truck. Stated goals for the prototype model are to reduce weight, enhance durability, control emissions, and increase engine performance. Electronics and hydraulics actuate the valves. A 40% increase in torque at clutch-engaging speeds is claimed. This provides smooth acceleration and quicker starts. From a drivability point of view, the design also provides greater control of deceleration, which reduces wear of wheel brake liners.
Both the inlet and exhaust valves are controlled by hydraulic actuation. This has the advantage of increasing valve seating and valve reliability while creating negligible noise. Solid state electronic control systems ensure reliability since these controls are more wear-resistant and are faster in action. Unlike mechanical systems, electronic controls are reliable and do not occupy much space and weight. Mechanical parts are add-on devices which increase the net weight and are subject to wear and tear. Smokeless diesel engines were introduced in 2004. Efforts are continuing to eliminate offensive fumes and odors. These are chemical reactions
Perennial problems in electronic and electrical devices
Electronic and electrical systems have problems. They attract dust particles which rigidly stick on the devices and keep on accumulating. Dust is an irritating nuisance. You can see it happening inside your computer, on electric fan blades, in air conditioners, and so on. Despite the high centrifugal force of fan blades, the dust clings on it forming a thick layer. Dust is nothing but charged particles which are attracted by an electrical field. The only way to avoid dust formation or accumulation is to apply an antistatic transparent lacquer coat.
Printed circuit boards are sensitive to heat. The working temperature of a diesel engine is 90 C. The electronic master devices are normally located inside the car dashboard where the air conditioner will help keep it cool. (Many trucks do not have air conditioners, but from a quality assurance standpoint, trucks with camless diesel engines will benefit from an air conditioner.) Despite providing heat protection for electronic and cables, dust accumulation at output points such as electronic actuators will eventually interfere with their smooth functioning. Periodical inspection is necessary.
Benefits of camless technology
· Torque at clutch-engagement speeds yields 40% increase in torque for smooth drive.
· Greater control over deceleration and less brake wear is caused by integration of compression braking technology.
· Hydraulic actuation causes gentle compression of the valves compared to the “mechanical shock” of cams and tappets.
· The camless system has no camshaft. This reduces the weight considerably.
· Solid state electronics function faster and easier. Low emissions reduce environmental damage