In a manufacturing setup, there will be different parameters for critical processes that have to be monitored. The real time values of these parameters will be fed to a central control system. These values are compared with the preset set-points through feedback systems and the necessary alerts are output on the display system, so that corrective action can be taken.
Representative process control system is one in which, a laser diode acts as the measuring device for detection of liquid/gas present in a given industrial environment.
The frequency signature of concerned material (liquid/gas) is then passed on to the receiver. It is then converted in digital form and picked by the processor.
The cost-performance trade off is to be balanced to implement application-specific peripherals for achieving the desired core performance.
Once the core is optimized for working with the desired peripherals, and speed, the rest of the system may be designed as per budget considerations.
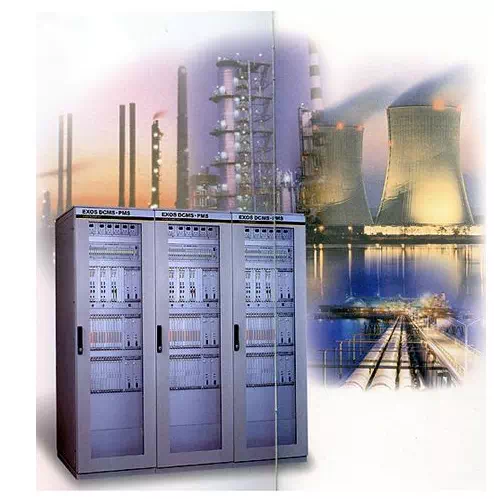
PLC and DCS: The Heart of Process Controls
The primary devices that are used in a process control system are Programmable Logic Controllers better known as PLCs in short. PLCs are the best bets for controlling machines with several discrete devices such as motor starters, limit switches, and the likes of them, which are often involved in automation process like material handling, state machines, sequencing, status reports etc.
Distributed Control Systems, commonly abbreviated as DCS, are central control systems, which are good at controlling analog devices; thereby aiding in process control.
In a manufacturing setup, feedback from different sensors tendering to many processes are given to a bank of PLCs. Each process has a separate set of PLCs and the output of these which contain information regarding the status at the shop floor is given to the DCS. PLC is just a controller and DCS is a central controller with a MMI [Man Machine Interface]. Corrective controls are input to the DCS, which is given to the PLC and thereafter sent to the individual control devices.
Modern PLCs & DCSs have enormous capability in a plant automation setting. There is good deal of difference in the capabilities of DCS as well as PLCs. DCS offers an integrated development environment which provides more powerful remote process control computers. DCS also functions as a supervising control which maintains quality at the desired level intended for the product.
Process Control Systems for Small Systems
For small systems a PLC+PC based system is perhaps the best possible solution, which may even supersede the goods delivered by a DCS.
Remember, DCS is however costlier than a PLC+PC based system. Scan times of PLCs are very less; so critical loops can be executed faster. However, PLCs do not have a rugged architecture and hence cannot be used for very large systems.
Dealing with Specific Inputs: Direct Digital Control
PLCs have to be programmed to output a particular function when given a set of specific inputs. The feedback of the process is accepted by the computer in discrete times and sample data, individually processed by many continuous analog and digital sensors, each working in its own statutory procedure.
In the direct digital control, the computer calculates the values of the input variables necessary to the process and transmits them to the program. The direct coupling of the process to the computer is called “direct digital control” which is an integral part of the process control system. The direct digital control coupled with the PLCs and DCS make the automation of any industrial setup very efficient and reliable.
In a Nutshell
So, there you have it – all about the process control systems. Additionally process control charts are used for representing the flow of work in a manufacturing set-up.
You can find a lot of valuable information in this process control systems shinskey PDF(you need to download it)
You may also read more on Pneumatic and Electronic Control Mechanisms and Access Control Systems here