1) Solid oxide fuel cells (SOFCs):
Solid oxide fuel cells (SOFCs) use a solid material, most commonly a ceramic material called yttria stabilized zirconia (YSZ), as the electrolyte. Because SOFCs are made entirely of solid materials, they are not limited to the flat plane configuration of other types of fuel cells and are often designed as rolled tubes. They require high operating temperatures (800–1000 °C) and can be run on a variety of fuels including natural gas.
SOFCs are unique since in those, negatively charged oxygen ions travel from the cathode (positive side of the fuel cell) to the anode (negative side of the fuel cell) instead of positively charged hydrogen ions travelling from the anode to the cathode, as is the case in all other types of fuel cells. Oxygen gas is fed through the cathode, where it absorbs electrons to create oxygen ions. The oxygen ions then travel through the electrolyte to react with hydrogen gas at the anode. The reaction at the anode produces electricity and water as by-products. Carbon dioxide may also be a by-product depending on the fuel, but the carbon emissions from an SOFC system are less than those from a fossil fuel combustion plant. The chemical reactions for the SOFC system can be expressed as follows
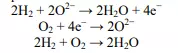
SOFC systems can run on fuels other than pure hydrogen gas. However, since hydrogen is necessary for the reactions listed above, the fuel selected must contain hydrogen atoms. For the fuel cell to operate, the fuel must be converted into pure hydrogen gas. SOFCs are capable of internally reforming light hydrocarbons such as methane (natural gas), propane and butane. These fuel cells are at an early stage of development.
Challenges exist in SOFC systems due to their high operating temperatures. One such challenge is the potential for carbon dust to build up on the anode, which slows down the internal reforming process. Research to address this “carbon coking” issue at the University of Pennsylvania has shown that the use of copper-based cermet (heat-resistant materials made of ceramic and metal) can reduce coking and the loss of performance. Another disadvantage of SOFC systems is slow start-up time, making SOFCs less useful for mobile applications. Despite these disadvantages, a high operating temperature provides an advantage by removing the need for a precious metal catalyst like platinum, thereby reducing cost. Additionally, waste heat from SOFC systems may be captured and reused, increasing the theoretical overall efficiency to as high as 80%–85%.
The high operating temperature is largely due to the physical properties of the YSZ electrolyte. As temperature decreases, so does the ionic conductivity of YSZ. Therefore, to obtain optimum performance of the fuel cell, a high operating temperature is required. According to their website, Ceres Power, a UK SOFC fuel cell manufacturer, has developed a method of reducing the operating temperature of their SOFC system to 500–600 degrees Celsius. They replaced the commonly used YSZ electrolyte with a CGO (cerium gadolinium oxide) electrolyte. The lower operating temperature allows them to use stainless steel instead of ceramic as the cell substrate, which reduces cost and start-up time of the system.
2) Hydrogen-Oxygen Fuel Cell:
The Hydrogen-Oxygen Fuel Cell was designed by Bacon in the year 1959. It was used as a primary source of electrical energy in the Apollo space program. The cell consists of two porous carbon electrodes impregnated with a suitable catalyst such as Pt, Ag, CoO, etc. The space between the two electrodes is filled with a concentrated solution of KOH or NaOH which serves as an electrolyte. 2H2 gas and O2 gas are bubbled into the electrolyte through the porous carbon electrodes. Thus the overall reaction involves the combination of hydrogen gas and oxygen gas to form water. The cell runs continuously until the reactant’s supply is exhausted. This type of cell operates efficiently in the temperature range 343 K to 413 K and provides a potential of about 0.9 V.
3) Molten carbonate fuel cells:
Molten carbonate fuel cells (MCFCs) require a high operating temperature, 650 °C (1,200 °F), similar to SOFCs. MCFCs use lithium potassium carbonate salt as an electrolyte, and this salt liquefies at high temperatures, allowing for the movement of charge within the cell – in this case, negative carbonate ions. Like SOFCs, MCFCs are capable of converting fossil fuel to a hydrogen-rich gas in the anode, eliminating the need to produce hydrogen externally. The reforming process creates CO 2emissions. MCFC-compatible fuels include natural gas, biogas and gas produced from coal. The hydrogen in the gas reacts with carbonate ions from the electrolyte to produce water, carbon dioxide, electrons and small amounts of other chemicals. The electrons travel through an external circuit creating electricity and return to the cathode. There, oxygen from the air and carbon dioxide recycled from the anode react with the electrons to form carbonate ions that replenish the electrolyte, completing the circuit.[43] The chemical reactions for an MCFC system can be expressed as follows:
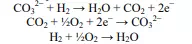
As with SOFCs, MCFC disadvantages include slow start-up times because of their high operating temperature. This makes MCFC systems not suitable for mobile applications, and this technology will most likely be used for stationary fuel cell purposes. The main challenge of MCFC technology is the cells’ short life span. The high-temperature and carbonate electrolyte lead to corrosion of the anode and cathode. These factors accelerate the degradation of MCFC components, decreasing the durability and cell life. Researchers are addressing this problem by exploring corrosion-resistant materials for components as well as fuel cell designs that may increase cell life without decreasing performance.
MCFCs hold several advantages over other fuel cell technologies, including their resistance to impurities. They are not prone to “carbon coking”, which refers to carbon build-up on the anode those results in reduced performance by slowing down the internal fuel reforming process. Therefore, carbon-rich fuels like gases made from coal are compatible with the system. The Department of Energy claims that coal, itself, might even be a fuel option in the future, assuming the system can be made resistant to impurities such as sulfur and particulates that result from converting coal into hydrogen.[34] MCFCs also have relatively high efficiencies. They can reach a fuel-to-electricity efficiency of 50%, considerably higher than the 37–42% efficiency of a phosphoric acid fuel cell plant. Efficiencies can be as high as 65% when the fuel cell is paired with a turbine and 85% if heat is captured and used in a Combined Heat and Power (CHP) system.
Fuel Cell Energy, a Connecticut-based fuel cell manufacturer, develops and sells MCFC fuel cells. The company says that their MCFC products range from 300 kW to 2.8 MW systems that achieve 47% electrical efficiency and can utilize CHP technology to obtain higher overall efficiencies. One product, the DFC-ERG, is combined with a gas turbine and, according to the company, it achieves an electrical efficiency of 65%.